Understanding AMS240X: What It Is and Why It Matters
Table of Contents
Introduction:
AMS240X is a standard that many industries use when working with coatings. If you have ever heard of AMS240X, you may wonder what it really means. In this blog, we will explore what AMS240X is, how it works, and why it’s important.
AMS240X is used in various industries like aerospace, automotive, and manufacturing. It provides guidelines for coating processes, ensuring that parts are coated properly. This standard helps make sure that the coatings on metals are done right, so the parts last longer and perform better.
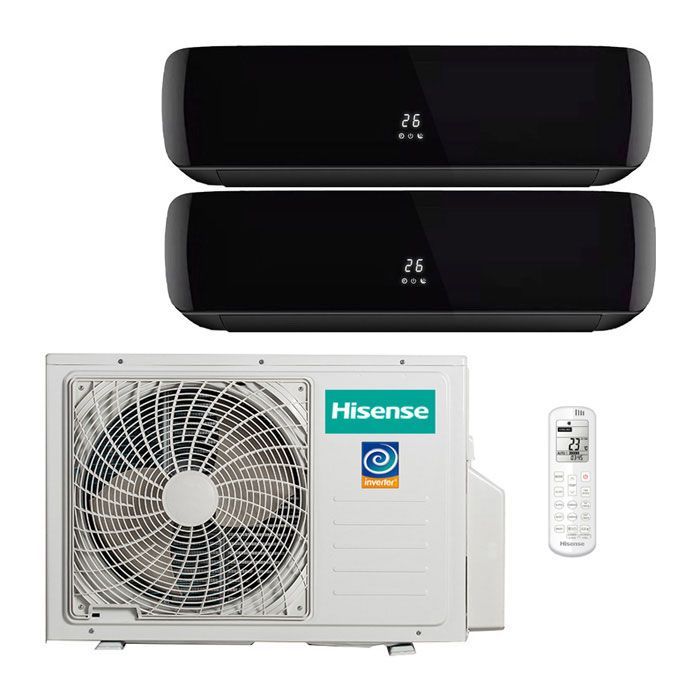
What is AMS240X and Why Is It Important?
AMS240X is a special standard used to make sure metal parts are coated properly. This standard provides clear instructions on how to apply protective coatings to metals, ensuring they are strong and last a long time. The main goal of AMS240X is to help industries create metal parts that resist damage from things like rust, wear, and corrosion. This is very important for making sure products stay safe and work well for a long time.
One of the key reasons AMS240X is so important is because it is used in industries like aerospace, automotive, and manufacturing. In these industries, metal parts need to be very strong and reliable. Without proper coatings, the parts could break down faster or even fail, leading to safety issues. By following AMS240X, companies can make sure their products meet high standards of durability and safety, which is important for both the companies and the people who use their products.
Another reason AMS240X is important is that it helps protect metal parts from harsh environments. For example, parts that are exposed to moisture or chemicals can rust quickly if they are not coated properly. AMS240X makes sure that the coating is thick enough and applied evenly so that the metal is well-protected. This helps the parts last longer and perform better, even in tough conditions.
AMS240X is also trusted because it helps reduce mistakes during the coating process. The guidelines in this standard tell companies exactly what materials to use and how to apply the coating. This means there is less chance of errors, like applying too little coating or using the wrong type of material. By following AMS240X, companies can be sure their parts will be coated correctly every time.
In conclusion, AMS240X is important because it helps ensure the quality, safety, and performance of metal parts across many industries. Whether it’s for airplanes, cars, or other machinery, using this standard helps companies make strong, reliable products that last longer and keep people safe.
How AMS240X Ensures Quality Coatings
AMS240X is a trusted standard that ensures metal parts receive high-quality coatings. It provides detailed instructions on how to properly coat metals, so they stay strong and resistant to damage. By following AMS240X, companies can apply coatings that protect metal parts from rust, wear, and other harmful effects. This makes the parts last longer and keeps them working well over time.
One of the ways AMS240X ensures quality is by giving clear guidelines on the thickness of the coating. A coating that is too thin might not protect the metal, while a coating that is too thick can affect the part’s performance. AMS240X helps companies apply the right amount of coating, making sure it’s just the right thickness to offer strong protection without causing problems.
Another way AMS240X guarantees quality is by requiring the use of specific materials for the coatings. The standard recommends materials like nickel, zinc, and chromium, which are known for their strength and resistance to corrosion. By using these high-quality materials, AMS240X ensures that the coatings can withstand harsh environments, such as extreme heat or moisture, without breaking down.
AMS240X also helps maintain quality by requiring regular testing of the coatings. After the coating is applied, it must be inspected to check if it meets the standard’s requirements. Testing includes checking the thickness of the coating, its adhesion to the metal, and its ability to resist corrosion. By following these testing steps, companies can be sure that the coating is effective and will protect the metal part for a long time.
In conclusion, AMS240X plays a key role in making sure metal parts receive high-quality coatings. By providing guidelines on coating thickness, materials, and testing, AMS240X helps companies create strong, durable products that can withstand tough conditions. This ensures the safety and performance of the metal parts, making them reliable for use in important industries like aerospace and automotive.
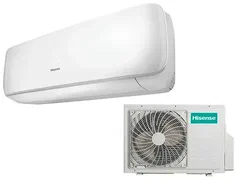
Industries That Use AMS240X Standards
AMS240X is a crucial standard used in many industries that rely on strong and durable metal parts. One of the main industries that use AMS240X is aerospace. In aerospace, the parts of airplanes, rockets, and other aircraft need to be tough and able to withstand extreme conditions, like high speeds and strong weather. The AMS240X standard helps make sure that these metal parts are coated properly, protecting them from rust and wear. This ensures the safety of the aircraft and the people who use them.
Another industry that relies heavily on AMS240X is the automotive industry. Cars, trucks, and buses are made with many metal parts that need to last a long time, even when exposed to rain, dirt, and heat. AMS240X coatings protect these parts, such as engines, brake systems, and chassis, from damage. By using the AMS240X standard, car manufacturers can make sure their vehicles are more durable, helping them stay on the road longer without needing repairs as often.
The electronics industry also uses AMS240X to protect important metal components. In electronics, parts like circuit boards and connectors can easily get damaged if they are not protected. The coatings that follow AMS240X standards help keep these parts safe from moisture and other things that can cause rust or damage. This is important because even small electronic parts can stop working if they are not well-protected, causing problems in devices like computers and phones.
Additionally, AMS240X is important in the manufacturing industry. Factories that make machines, tools, and equipment use metal parts that need to be strong and reliable. These parts often come in contact with heavy machinery or chemicals that can cause wear and tear. AMS240X coatings provide a protective layer that keeps these parts from breaking down, allowing them to function properly for a longer period of time. This saves manufacturers time and money by reducing the need for frequent repairs or replacements.
In conclusion, AMS240X is used in a wide range of industries, including aerospace, automotive, electronics, and manufacturing. These industries depend on the AMS240X standard to make sure their metal parts are coated well and last longer. The standard helps protect metal from damage, ensuring that the products made in these industries are safe, durable, and high-quality.
Benefits of Following AMS240X for Coatings
Following AMS240X standards for coatings brings many important benefits, especially for industries that use metal parts. One of the biggest advantages is the protection it provides against rust and corrosion. Metal parts that are coated according to AMS240X are much more resistant to damage caused by moisture, chemicals, and other harsh conditions. This ensures that the parts last longer, reducing the need for frequent replacements and helping products stay in good condition.
Another benefit of AMS240X is that it improves the overall quality and strength of metal products. The standard makes sure that the coatings are applied evenly and with the right thickness, which keeps the metal strong. Products coated with AMS240X are more durable and can handle tough environments, such as high heat or pressure. This makes them more reliable, whether they’re used in airplanes, cars, or machinery.
AMS240X also helps save money in the long run. When companies use this standard, their products last longer and don’t need to be repaired or replaced as often. This reduces maintenance costs for both manufacturers and customers. By investing in proper coatings from the start, businesses can avoid expensive problems in the future, such as metal parts failing or breaking down too soon.
In addition to these practical benefits, following AMS240X ensures safety. Metal parts that follow this standard are protected from wear and damage, which helps prevent accidents or failures. This is especially important in industries like aerospace and automotive, where the safety of the people using these products is a top priority. By using AMS240X, companies can make sure their products meet high safety standards.
In conclusion, AMS240X offers many benefits, including better protection against rust, stronger and more durable products, cost savings, and improved safety. By following this standard, companies can produce high-quality, long-lasting metal parts that perform well in a variety of industries. This makes AMS240X an essential standard for businesses that want to create reliable and effective products.
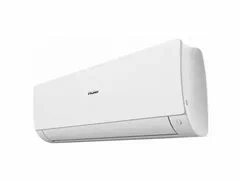
The Role of AMS240X in Aerospace Applications
AMS240X plays a very important role in aerospace applications by ensuring that metal parts used in aircraft are well-protected and durable. In the aerospace industry, safety and reliability are top priorities, as even the smallest part failure can have serious consequences. AMS240X helps prevent these failures by providing a standard for applying protective coatings to metal components, making them more resistant to corrosion, rust, and wear.
One of the main reasons AMS240X is crucial in aerospace is that airplanes and other aircraft operate in harsh environments. They face extreme temperatures, high speeds, and exposure to moisture and chemicals. Metal parts, such as landing gears, engines, and wings, must be able to withstand these conditions without breaking down. By following AMS240X standards, companies can apply coatings that protect these critical parts, ensuring the aircraft’s overall safety and performance.
Another key role AMS240X plays in aerospace is extending the lifespan of aircraft parts. Aircraft are expensive to build and maintain, so it’s essential for parts to last as long as possible. The coatings applied using AMS240X protect metal parts from damage, which helps prevent the need for frequent replacements or repairs. This not only saves money but also ensures that planes stay in operation longer, which is especially important for airlines and defense companies.
Additionally, AMS240X helps maintain the high standards required in aerospace manufacturing. The standard provides specific guidelines for the type of coatings to use, the thickness of the coating, and how it should be applied. This consistency is vital for ensuring that all parts are coated the same way, reducing the risk of mistakes that could lead to part failures. By following AMS240X, aerospace companies can be confident that their parts meet the strict quality requirements needed for safe flight.
In conclusion, AMS240X plays a critical role in aerospace by ensuring that metal parts are coated properly to resist damage and last longer. This standard helps aircraft withstand tough environments, reduces maintenance costs, and improves safety. By using AMS240X, aerospace companies can produce reliable, high-quality parts that meet the industry’s demanding requirements.
AMS240X in Automotive Industry: Why It Matters
AMS240X plays an important role in the automotive industry, where durability and safety are essential. Metal parts in cars, trucks, and other vehicles must be strong enough to withstand daily use and tough conditions like heat, moisture, and road wear. By following AMS240X standards, automotive manufacturers ensure that metal parts are coated properly, providing extra protection against rust and corrosion. This helps vehicles stay reliable and last longer on the road.
One of the key reasons AMS240X matters in the automotive industry is its ability to extend the lifespan of metal parts. Car parts, such as the engine, brake components, and exhaust systems, are exposed to a variety of harsh elements. By using AMS240X-approved coatings, manufacturers can protect these parts from damage. This reduces the need for repairs and replacements, helping cars perform well over time and saving drivers money on maintenance.
Another reason AMS240X is so important in automotive applications is that it helps improve safety. Vehicles rely on the strength and functionality of their metal parts to operate safely. For example, brake systems and steering components must remain in excellent condition to prevent accidents. The coatings applied using AMS240X ensure that these parts stay protected from corrosion and wear, reducing the risk of failures and enhancing the safety of the vehicle.
AMS240X also supports quality and consistency in automotive manufacturing. The standard provides clear guidelines on the type of coating, thickness, and application process to follow. This helps ensure that all metal parts are treated the same way, resulting in reliable performance across different vehicles. Whether it’s a small car or a heavy-duty truck, AMS240X ensures that the metal components meet high-quality standards.
In conclusion, AMS240X is vital in the automotive industry because it protects metal parts from rust, extends their lifespan, and ensures vehicle safety. By following this standard, automotive manufacturers can produce durable, high-quality cars and trucks that drivers can rely on. This makes AMS240X an essential part of keeping vehicles running smoothly and safely for years to come.
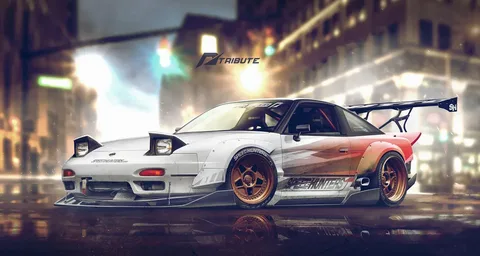
Common Materials and Coatings Under AMS240X
AMS240X provides guidelines for the application of various coatings to metal parts, using materials that are well-known for their durability and resistance to corrosion. Some of the most common materials used in AMS240X coatings include nickel, zinc, and chromium. These materials are highly effective in protecting metal parts from rust and wear, making them ideal for industries such as aerospace, automotive, and manufacturing.
Nickel is one of the most popular materials used in AMS240X coatings. It offers excellent resistance to corrosion, especially in harsh environments such as high temperatures and exposure to moisture. Nickel coatings are often applied to metal parts like engine components, electrical contacts, and machinery parts. The coating provides a protective barrier, ensuring the metal parts stay strong and functional for longer periods.
Zinc is another common material used in AMS240X coatings, particularly for its ability to prevent corrosion. Zinc coatings are widely used on steel and iron parts, providing a layer of protection that helps prevent rust. This makes zinc coatings a common choice in automotive and construction industries, where metal parts are constantly exposed to the elements. Zinc coatings are applied through a process called galvanizing, which makes the metal parts more durable and resistant to the wear and tear of daily use.
Chromium is also frequently used in AMS240X coatings, known for its hardness and resistance to scratches and wear. Chromium coatings are commonly applied to automotive and aerospace components, such as wheels, pistons, and turbine blades. Chromium not only protects the metal from corrosion but also gives it a shiny, attractive finish. This makes it a popular choice for parts that need both durability and a polished appearance.
In conclusion, AMS240X covers a range of materials and coatings that are essential for protecting metal parts. Nickel, zinc, and chromium are some of the most commonly used materials, each offering unique benefits like corrosion resistance, durability, and strength. By following AMS240X, industries can ensure their metal parts are coated properly, extending their lifespan and improving their performance.
How AMS240X Impacts Product Durability
AMS240X has a significant impact on the durability of metal products by ensuring that they are coated with the right materials and techniques. Coatings that follow AMS240X standards help protect metal parts from various forms of damage, including rust, corrosion, and wear. This protection is essential for extending the life of metal components used in industries such as aerospace, automotive, and manufacturing. By following AMS240X, manufacturers can produce products that remain strong and functional over time, even when exposed to harsh conditions.
One of the main ways AMS240X impacts product durability is by providing a protective barrier against environmental factors. Metal parts, especially those used in outdoor or industrial environments, are often exposed to moisture, heat, and chemicals. These elements can cause the metal to corrode or weaken over time. However, AMS240X coatings are designed to protect metal surfaces from these damaging factors, ensuring that the parts remain durable and reliable for a longer period.
Additionally, AMS240X coatings improve the mechanical strength of metal products. The coatings create a tough outer layer that can withstand friction, impact, and other stresses that might otherwise cause the metal to wear down. This is especially important for parts like engines, gears, and brakes, which experience constant pressure and movement. By following AMS240X standards, manufacturers can make sure these parts are more resilient and less likely to fail due to wear and tear, which is essential for maintaining the durability of the entire product.
Another way AMS240X impacts durability is by reducing the need for frequent maintenance or repairs. Products coated according to AMS240X standards last longer, which means less downtime for repairs and replacements. For example, in industries like automotive and aerospace, parts that follow AMS240X are less likely to corrode or degrade, reducing the overall maintenance costs. This makes AMS240X coatings a cost-effective way to enhance product durability and save money in the long run.
In conclusion, AMS240X plays a key role in enhancing the durability of metal products. By providing protection against environmental damage, improving mechanical strength, and reducing maintenance needs, AMS240X helps ensure that metal parts last longer and perform better. Industries that use AMS240X coatings can rely on their products to be more durable, saving time and money while maintaining high performance over time.
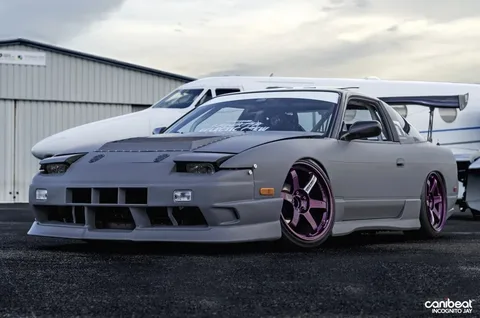
Steps Involved in the AMS240X Coating Process
The AMS240X coating process involves several important steps to ensure that metal parts are coated properly and effectively. These steps are designed to provide maximum protection against corrosion and wear, making the metal parts more durable. The first step in the process is cleaning the metal parts. This is crucial because any dirt, grease, or other contaminants on the surface can prevent the coating from bonding properly. The cleaning is typically done using chemical solutions or abrasive materials to remove all impurities.
Once the parts are cleaned, the next step is to prepare the metal surface for coating. This is often done by etching or roughening the surface to create a better bond between the coating and the metal. This step is essential because a smooth or untreated surface can cause the coating to peel or wear off quickly. By ensuring the surface is properly prepared, the coating will adhere better and provide long-lasting protection.
After surface preparation, the next step in the AMS240X coating process is applying the coating itself. Depending on the material being used, this can be done through several methods, such as electroplating, spray coating, or immersion. The type of coating material used, like nickel, zinc, or chromium, will depend on the specific requirements of the part and its intended use. The coating is applied in a controlled environment to ensure an even and consistent layer across the entire surface of the part.
Once the coating is applied, it needs to be cured or hardened. This is usually done by heating the coated parts in an oven or using another method to allow the coating to set properly. Curing ensures that the coating has the strength and durability required to protect the metal part from corrosion and wear. It also helps the coating bond firmly to the metal, making it more resistant to peeling or chipping.
In conclusion, the AMS240X coating process is a series of well-defined steps designed to ensure the metal parts are properly coated and protected. These steps include cleaning, surface preparation, coating application, and curing. Each step is crucial for achieving the best possible results and ensuring the parts have the durability needed to withstand harsh conditions. Following the AMS240X process helps produce high-quality, long-lasting coated metal parts for a variety of industries.
AMS240X: Ensuring Safety and Performance in Manufacturing
AMS240X plays a crucial role in ensuring safety and performance in manufacturing by providing a clear standard for coating metal parts. In industries such as aerospace, automotive, and heavy machinery, metal components are constantly exposed to harsh conditions like moisture, extreme temperatures, and friction. These factors can weaken parts over time, leading to potential failures that could compromise safety and performance. AMS240X ensures that metal parts are coated with protective layers that help them resist these damaging elements, allowing them to function safely and effectively for longer periods.
One way AMS240X ensures safety is by improving the corrosion resistance of metal parts. When metal parts are exposed to moisture, they are at risk of rusting, which can weaken their structure and make them unsafe to use. By following AMS240X guidelines for coating, manufacturers can apply materials like zinc, nickel, or chromium to protect metal surfaces from corrosion. This reduces the likelihood of part failure and helps keep the final product safe for use in critical applications, such as in aircraft or vehicles where safety is a top priority.
In addition to corrosion resistance, AMS240X also contributes to the overall performance of metal parts. The coatings applied using AMS240X standards not only protect against rust but also enhance the durability and strength of the metal. This is particularly important in high-stress environments, where parts need to withstand heavy wear and tear. For example, engine components, brakes, and gears all benefit from AMS240X coatings, which ensure they remain functional and reliable over time, even under extreme conditions.
Another way AMS240X impacts safety and performance is by promoting consistency in manufacturing processes. The standard provides detailed guidelines on how to apply coatings to metal parts, ensuring that the same high-quality results are achieved every time. This consistency reduces the risk of defects or variations that could affect the part’s performance or safety. Manufacturers can rely on AMS240X to produce uniform, high-quality parts that meet strict industry standards for safety and functionality.
In conclusion, AMS240X is vital for ensuring both safety and performance in manufacturing. By providing clear guidelines for coating metal parts, it helps protect them from corrosion, enhances their strength, and ensures they function reliably over time. Following AMS240X standards gives manufacturers the confidence that their products will meet high safety and performance standards, making it an essential part of the manufacturing process.
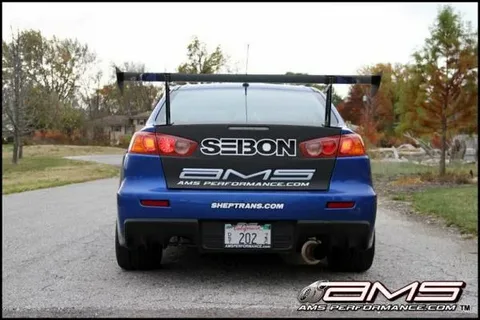
Why AMS240X Is the Standard for Metal Coatings
AMS240X has become the standard for metal coatings due to its ability to ensure high-quality, reliable, and durable coatings for metal parts. This standard sets clear guidelines for applying protective coatings to metals, making it a trusted reference in various industries such as aerospace, automotive, and manufacturing. By following AMS240X, manufacturers can ensure that their products meet high performance and safety standards, which is why it is widely recognized as the go-to standard for metal coatings.
One of the main reasons AMS240X is considered the standard is its focus on corrosion resistance. Metal parts are vulnerable to rust and corrosion when exposed to moisture, chemicals, or other harsh conditions. AMS240X addresses this issue by recommending coatings that protect the metal from these environmental factors. Materials such as nickel, zinc, and chromium, which are commonly used in AMS240X coatings, form a strong barrier that prevents corrosion and extends the life of the metal parts. This makes AMS240X essential for industries where the reliability and durability of metal components are critical.
AMS240X is also the standard because it promotes consistency and quality control in manufacturing. The guidelines within AMS240X ensure that the coating process is uniform and reliable. By following the steps outlined in the standard, manufacturers can ensure that the coatings applied to metal parts meet the same high quality each time. This consistency is especially important in industries like aerospace and automotive, where even small variations in coating thickness or quality can affect the performance and safety of the product.
In addition to its focus on corrosion resistance and consistency, AMS240X is known for its versatility. The standard covers a wide range of metal coatings for different types of metal and applications. Whether it’s for parts used in high-temperature environments, heavy machinery, or delicate electronic components, AMS240X provides the necessary guidelines to ensure the right coating is applied. This adaptability makes AMS240X a valuable resource for various industries, ensuring that metal parts are protected and perform well across a wide range of conditions.
In conclusion, AMS240X is the standard for metal coatings because it provides clear, reliable, and consistent guidelines that ensure the durability and performance of metal parts. Its focus on corrosion resistance, quality control, and versatility makes it a vital reference for industries where metal parts need to withstand tough conditions. By following AMS240X, manufacturers can be confident that their products will meet high standards of quality and reliability, making it the preferred choice in metal coating applications.
AMS240X: Frequently Asked Questions and Answers
AMS240X is a widely used standard for metal coatings, and many manufacturers and industries rely on it for its clear guidelines and trusted results. However, there are often questions about the standard, its purpose, and how it is applied. In this section, we will address some of the most frequently asked questions about AMS240X to help clarify its importance and role in metal coating processes.
What is AMS240X?
AMS240X is a set of guidelines developed by the Society of Automotive Engineers (SAE) that outlines the requirements for metal coatings, specifically focusing on protective coatings like nickel, zinc, and chromium. The standard defines the methods and materials used for coating metal parts to enhance their durability and protect them from corrosion. By following AMS240X, manufacturers can ensure that their products meet high standards of performance and longevity, especially in industries where metal parts are exposed to harsh environments.
Why is AMS240X important?
AMS240X is crucial because it ensures that metal coatings provide reliable protection against corrosion and other forms of damage. Metals exposed to moisture, chemicals, or extreme temperatures can degrade over time, but coatings applied according to AMS240X guidelines help to prevent this. The standard promotes consistency, durability, and quality control, which are essential for industries such as aerospace, automotive, and manufacturing. By following AMS240X, manufacturers can produce metal parts that last longer and perform better, reducing the need for repairs or replacements.
How do I apply AMS240X coatings?
The process of applying coatings under AMS240X involves several steps, including cleaning the metal surface, preparing it for coating, applying the coating itself, and curing it. Depending on the material being used, coatings can be applied using methods such as electroplating, spray coating, or immersion. It is essential to follow the AMS240X guidelines at each step to ensure that the coating adheres correctly and provides the necessary protection. Manufacturers typically work with coating specialists or use automated systems designed to meet AMS240X standards.
Can AMS240X be used for all types of metal parts?
Yes, AMS240X is versatile and can be applied to various types of metal parts, including those made from steel, aluminum, and titanium. The standard covers coatings for different applications, whether for parts exposed to extreme temperatures, heavy wear, or moisture. While AMS240X is most commonly used in industries like aerospace and automotive, its adaptability makes it suitable for a wide range of manufacturing processes, ensuring metal parts are protected in diverse conditions.
In conclusion, AMS240X is a vital standard for metal coatings, providing manufacturers with a reliable set of guidelines to ensure their metal parts are durable, corrosion-resistant, and high-performing. By addressing common questions about AMS240X, it becomes clear why this standard is essential for producing high-quality, long-lasting metal products across various industries.
Conclusion
In conclusion, AMS240X is an important standard for making sure metal parts are coated properly. It helps companies in many industries, like aerospace and automotive, make strong and long-lasting products. By following AMS240X, the parts can resist rust and damage, making them safer to use. This standard is trusted because it makes sure coatings are applied the right way every time.
Overall, using AMS240X helps improve the quality of products and keeps them working well for a long time. Companies that follow this standard can be sure their products are safe and reliable. Whether it’s an airplane or a car, AMS240X makes sure the metal parts are protected and ready for tough jobs.
Post Comment